Designing with Autodesk Fusion 360
I'm just so impressed with Fusion 360. It's an amazing CAD tool, and not at all difficult to learn. A few hours watching Youtube tutorials and I soon picked it up. But its not just designing the parts, its thinking through the what if's, how will something you design perform? Will it fit? What material is best? How much will it weigh and does it weigh less that what it's replacing? Will it actually work? Whats the cost to manufacture, can it be manufactured, and can that cost be reduced by reducing the complexity?I use 3D People (3D printing) for manufacturing. The best results are when SLS printing is chose in Nylon PA12
Fusion 360 plugins
I use airfoil tools plug-in for Fusion 360. This allows you to draw aerodynamic airfoils very easily. There is a very good demonstration on youtube. Using this plug-in I've created several models that have been 3D printed, including a vortex generator and a turning vane.Aero
Turning vane (Nylon PA12 SLS printed)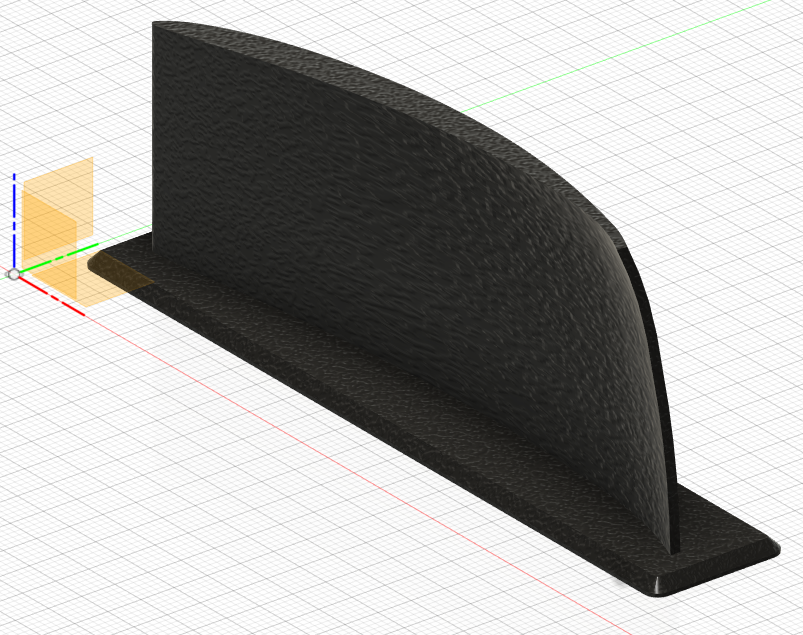
Vortex generator (Nylon PA12 SLS printed)
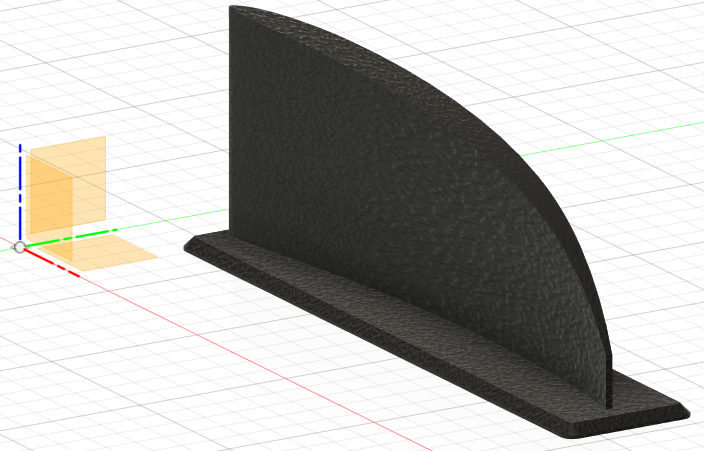
Diffuser louvres (Nylon PA12 SLS printed)

Suspension
Carbon camber shim (CNC machined 1mm carbon sheet)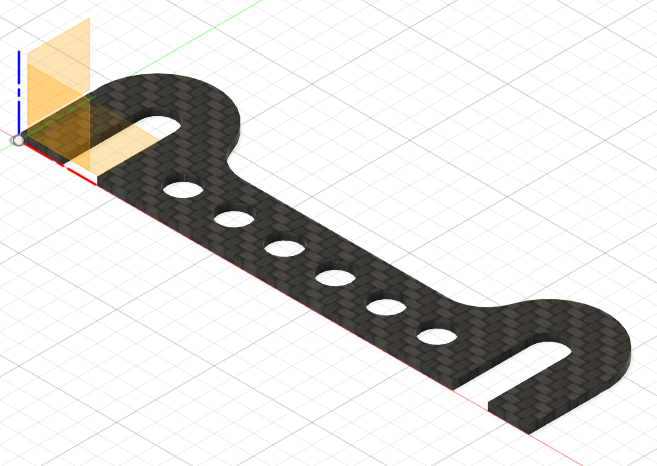
Rear suspension rocker (CNC machined)
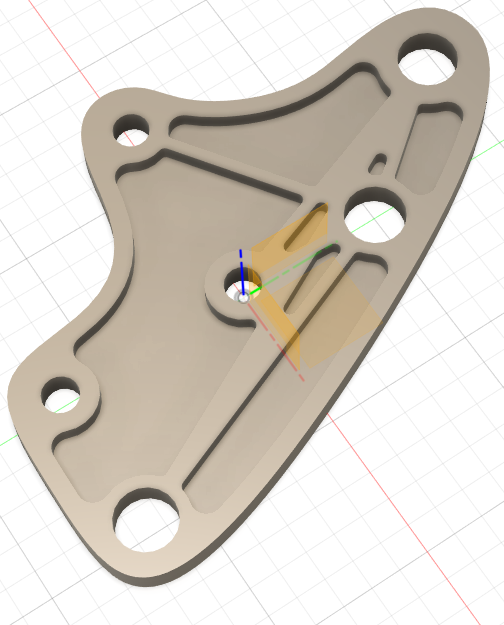
Uprated forward lower front suspension (CNC machined)

Uprated rearward lower front suspension (CNC machined)
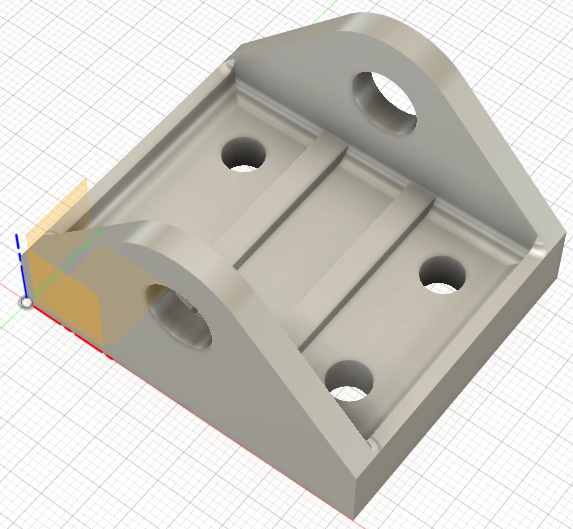
Supports
Rear wing supports (CNC machined from 6082T1 aluminium)These are CNC machined from 6mm 6082 T6 aluminium, finished to 3.2µm, polished and then anodized black. They are 2mm thick in the milled out sections, and weigh approx 600g each. The brackets they replaced weighed 1kg each, so I saved 800g. I profiled all the edges to make them as aerodynamic as possible. This, together with the milled out centre sections, made them very expensive to manufacture. But the quality from the supplier, Fractory, is outstanding.
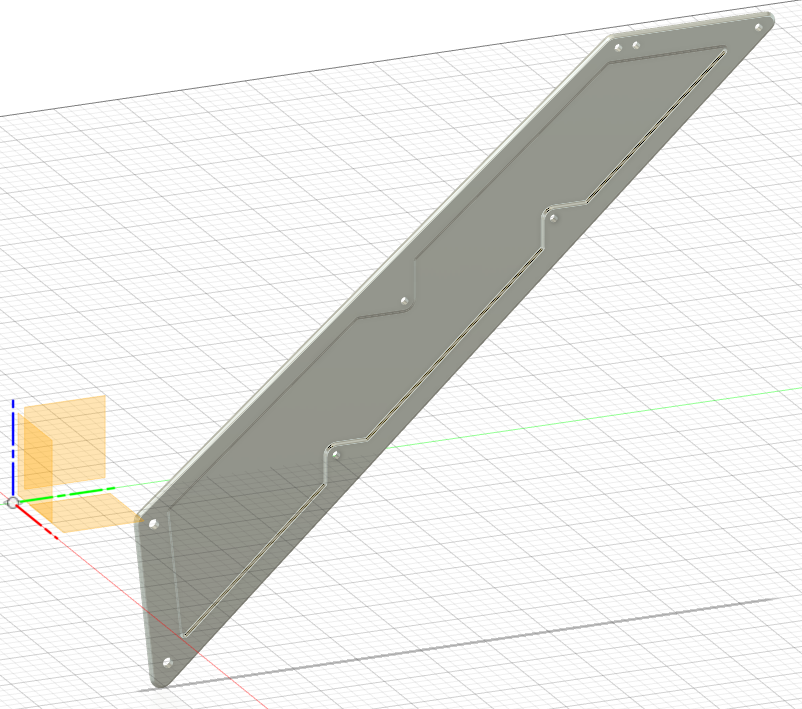
Damper reservoir support (Onyx CFS SLS printed)
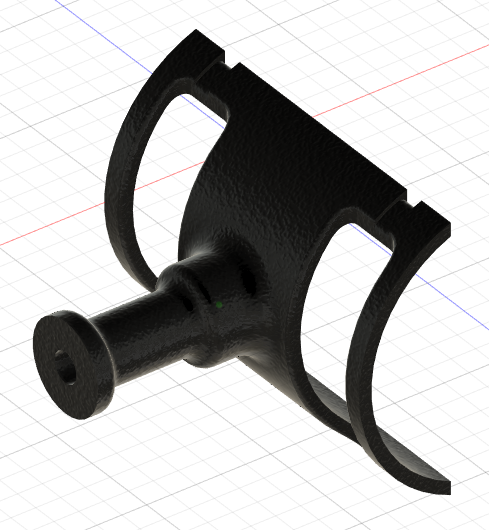
Bosch linear sensor collar clamp (Nylon PA12 SLS printed)
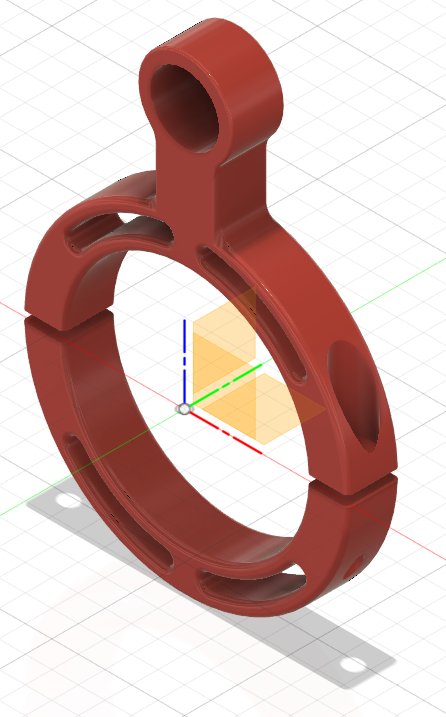
Bosch linear sensor rod end post (Nylon PA12 SLS printed)
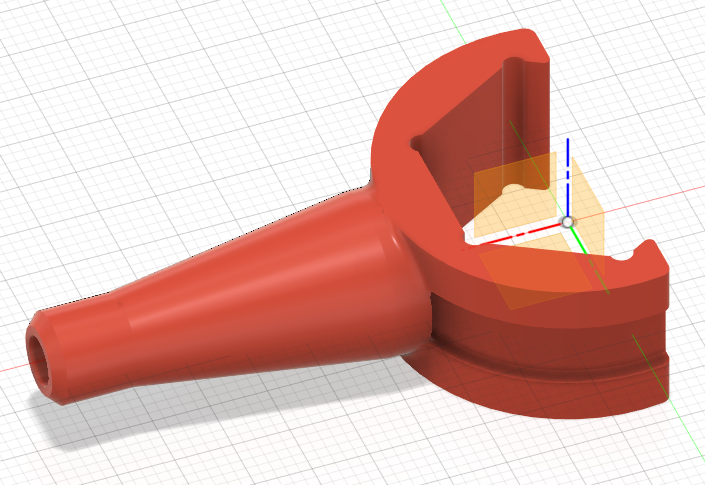
FTR 16tooth reluctance ring (Laser cut steel)
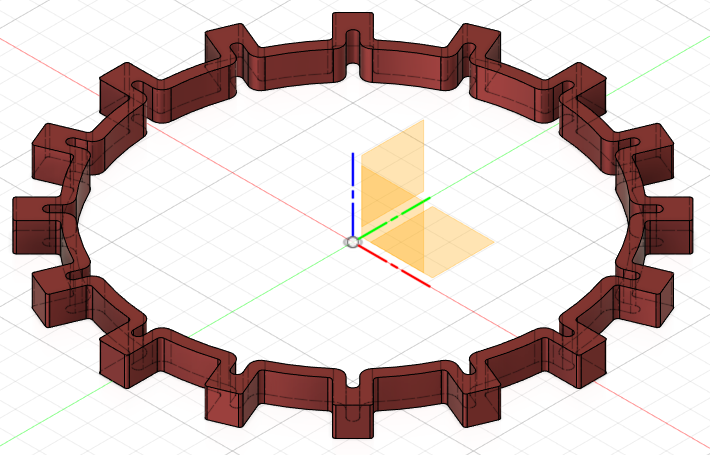
Radical SR3 printed reluctance ring, which uses 4mm steel dowels pressed in to the ring.

CNC machined front wing drop plates, shortened, and less complex than the first ones I designed, which reduces the manufactring costs.

Force TA cooling louvres, designed for the 2024 championship winning car to aid cooling.

A bezel for the Plex SDM-330 display, for mounting on a Sparco steering wheel.

Hewland FTR CNC machined stubby dry sump oil return pot with 3D printed cap and breather hole
