Latest News
17July
Coming up - Croft sprint
I'm looking forwards to the upcoming trip to Croft for round four of the Javelin sprint championship on July 27th. I am leading the championship, but I'm missing both the Anglesey rounds in September due to a surgical procedure I've got booked the last week in August, so the Blyton sprint in August (16th & 17th) will probably be the last time I drive the car this year. Missing the remaining rounds means I cant win the championship overall, but I'm not too bothered about that, I just want to enjoy the car and the driving.In prep for Croft I've changed the dashboard layout, to reduce clutter from the Pits screen, and increase the intensity of the LED's from 10% to 90%, I just couldn't see them at Cadwell. The 3D printed bezel worked great, and the joystick I found made it very easy to change screens. Its a very impressive dashboard, well worth looking at if you're in the market for one.
16July
Noise issues at Lydden Hill
The organisers had to alternate race cars with saloon cars at one point last Saturday, due to noise issues at the track, and that meant the fourth timed runs were cancelled. I have heard stories of residents sitting outside their homes with sound meters, monitoring the noise levels. I'm sure the track was there before they occupied their homes.Broughton took two wins, with Jones 2nd, and the rest were several seconds slower. I believe Nick Scott has now hung up his helmet, he is apparently selling his Force, which means one less driver heading over to N.Ireland in August. I reckon there's going to be just five drivers heading over this year. Easy points for those who do, 80 points for the weekend for the sixth place driver just for turning up; my money is on the local Ethan Faulkner to clean up both days.
11July
Falling attendance
Just ten drivers travelling to the next BSC round at the weekend, at Lydden Hill. Thats one less than 2024. I wonder how few will travel across to Kirkistown in August? I mean its easy points when no one else turns up. No qualifying, just drive it and net a bag of points for showing up. I wish the championship would revert back to the old points system, with Top 12 run offs.9July
Two more weekends remain
I've only got two more events to go this year; the Javelin sprint at Croft at the end of July, and the Yorks motor club event at Blyton in August, both of which I am really looking forward to. I'm not planning on racing after August, the new job is very time consuming with lots of travel, and therefore very tiring.29June
Cadwell success
I managed one practice and five timed runs yesterday, getting my time down to an 82.21s run on the old pirellis. That was good enough for first in class and FTD. This is only my 3rd visit to Cadwell in the Mygale, and only the second full dry event. The first visit in 2023 was wet, and in 2024 I managed a 82.54s run. Today I took 0.3s off that time which given the extreme temperatures I was quite happy with.The Plex dash worked perfectly, allowing me to see all the channels, and select gears using the paddles. Aside from the bonkers 30 degree heat, it was a very enjoyable day, blasting around the Cadwell Park circuit. I've still not learnt it, but I was making huge improvements, getting more and more confident. Again, swapping from the two year old Avons to Pirellis gave a big improvement in grip on the final two runs, and it was only then that I could really push the car.
27June
Cadwell this Saturday
The car is all packed up and ready for the trip over this afternoon, for the JTSS competition at Cadwell Park tomorrow. Just hope I can get a decent spot in the tarmac paddock.Plex has featured my dashboard install on their web site, it's a very impressive read.
Plex SDM-330 article
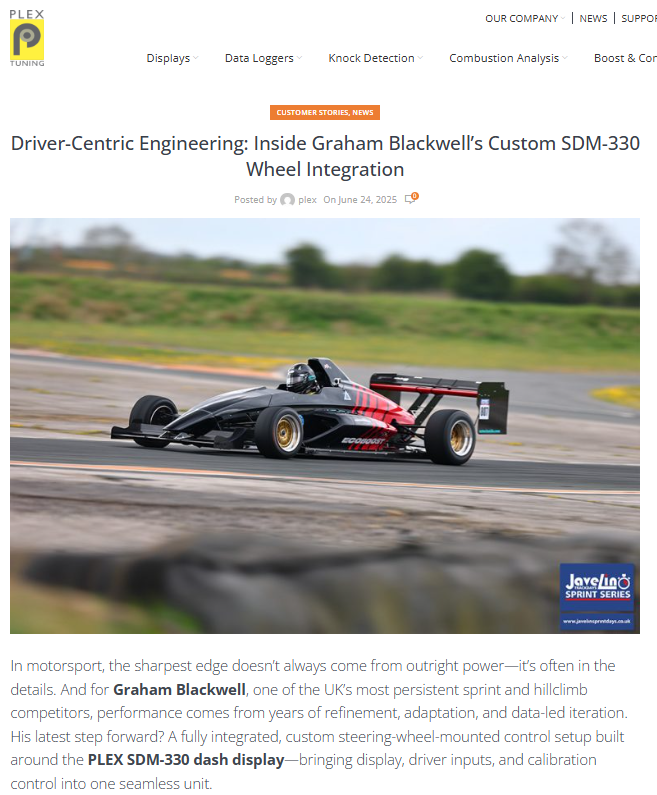
22June
Mallory Park BSC round 13 & 14
I went to Mallory Park on Saturday, to watch Ethan Faulkner pedal his OMS around the circuit, and I wasnt disappointed. He managed a 2nd place in the one and only run off in the afternoon, proving how adept he is at learning tracks. This was his first visit to the Leicestershire circuit.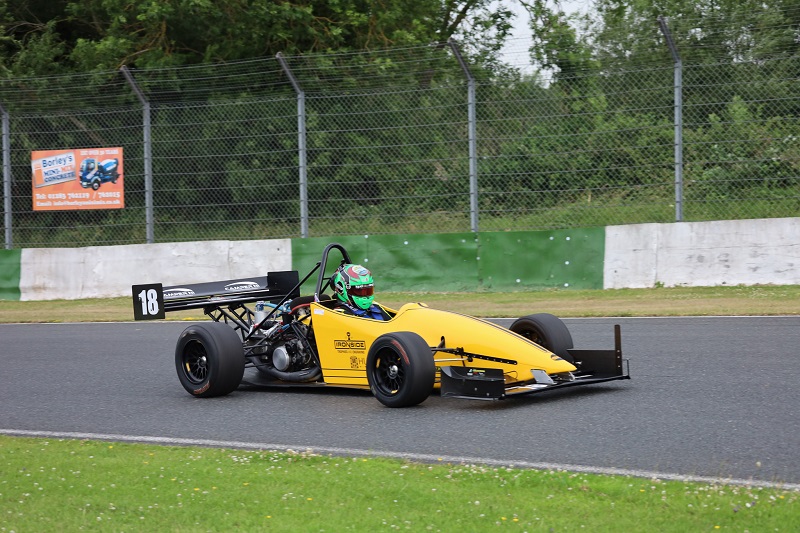
It was another day beset with problems. Mallory Park just doesnt seem to lend itself to smooth running sprints over the two lap format (not when there are multiple accidents anyway). The circuit is great, but the venue desperately needs a revamp! A drastic shortage of marshals, and temperatures peaking at 29C didnt help. A crash in the morning involving a Lotus delayed proceedings by 30 or so minutes. A couple of rain showers made things interesting, and after the commencement of the T2 run after lunch, the BSC drivers had just completed their runs at the head of the batch, when a further short shower made the track very damp, sadly catching out one of the Radical drivers. As they crossed the finish line, braking heavily, the car did a 180 and then hit the tyre barrier on the left just after the Edwina chicane. The driver was carted off to the medical centre, and after an hour the organisers announced the meeting had been abandoned since the ambulance needed to leave the circuit to take the driver to Leicester Royal Infirmary for further checks.
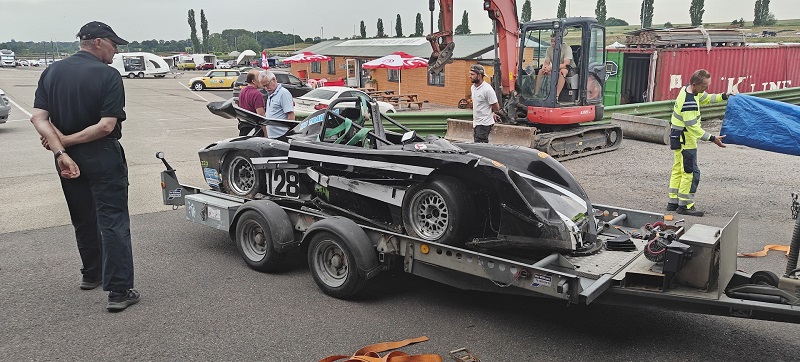
I was sat in the cafe downloading images from my camera when I heard the impact. It sounded horrible. When I looked across the track, the driver appeared to sit for quite a while before anyone turned up. A young marshal was first on the scene, and others soon followed. The tyres on that tyre wall made short work of the Radical. I dont know how old the tyres are, but they're bound together tightly, and have gone very hard having sat exposed to the elements for many years, and they just dont offer the protection of recticel/foam barriers.
I hope the driver recovers quickly, and gets back behind the wheel again soon.
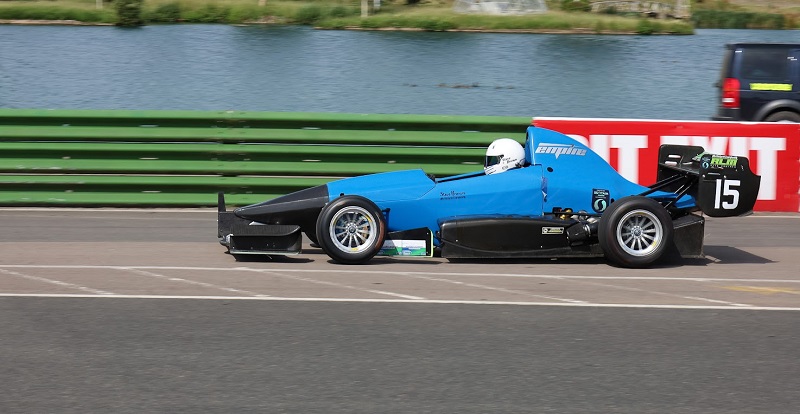
As for the eleven BSC drivers, Steve Browns supercharger failed on the Empire EVO at the end of his first practice run, leading to him missing the T1 qualifier run whilst he swapped chargers over. Steve Broughton's gearbox shat itself on the line in practice, and he also missed the T1 run, but had the car running for the one and only run off. It was good to see the new F4 EcoBoost running. It sounds and looks like it needs a lot of work on the tuning, particularly with the launch control as it often bogged down and stalled on the line. But they've only just started the journey so I'm sure they'll get it running smoothly in time.
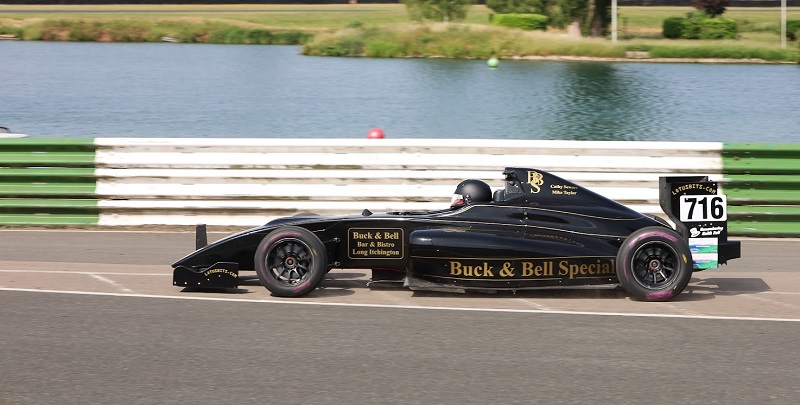
There was another EcoBoost, the ex-Sutton car, running around at the back of the group, so aside from Smiles and Ethan, Pete G wasnt really troubled and picked up yet another win. Chris Jones had COVID, so he sadly missed the event, which he may regret later in the year. I had a few welcomes, good to see you's, and a very frosty 'youre not welcome here' from one of the more senior drivers; it's a championship with a definite PR problem.
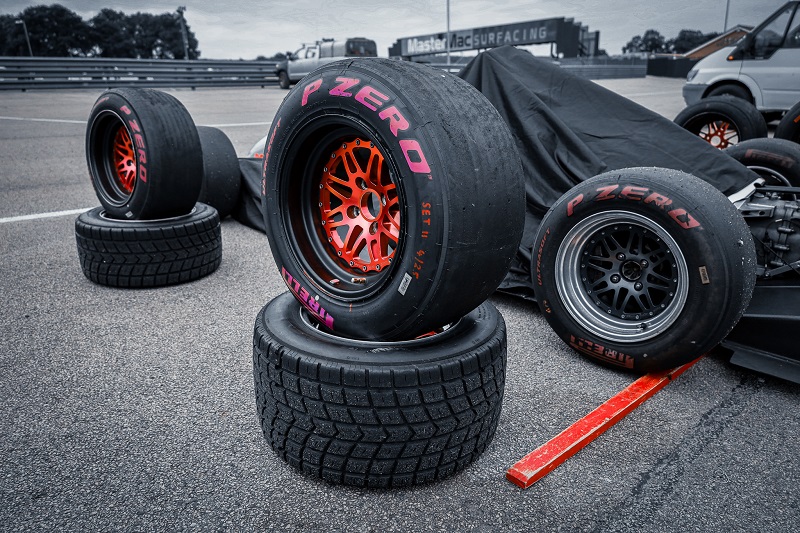
14June
Tyres cleaned
I cleaned the Pirellis today, which are 3 years old but still have loads of life left in them. I'm going to fit the new Pirellis to the other set of rims, to replace the two year old Avons. Just trying to find someone in Leicester that can fit tyres to split rims, after the last experience where one particular shop managed to bend an outer, I'm just not sure who to take them to. I asked Graham Goodes but they declined. I may have to take a trip over to BMTR if I cant find anyone locally. Thats not too bad as they're 45 minutes away, but it'd be easier to find someone local.I'm at Cadwell Park on the 29th June, so I need to get the fresh rubber fitted before then.
Plex are going to write a feature on my 3D printed dashboard solution for the SDM-330. I've been asked to provide photographs and some notes on what I've achieved, so hopefully I'll be sharing a link to their web site in the next week or so.
9June
Extra CAN
I added four more channels to the Life ECU Datastream, as it was still only sending 48 channels (48 is the maximum the Dash4Pro could work with). I've added gpsTimeHour and gpsTimeMin, as well as engineEnable, and LaunchMode.The reason for adding the pair of gps channels, is that I now have a digital clock on the pits/paddock page, so when the engine is idling and I'm either warming the engine up or sat in the car in the queue, I can a) see the time, and b) have confirmation that the GPS board has aquired a satellite lock and therefore the car will have a track map for me to download when the run is complete.
engineEnable is used for a new icon, which shows if the ignition is on or off. I had to create a flag and invert the logic, because the channel returns 0 for igntion on, and 1 for off. The reason for that is the ECU needed a 1 to kill the engine when the switch is turned off, so the ECU outputs the reverse to what you think it would for ignition on and off.
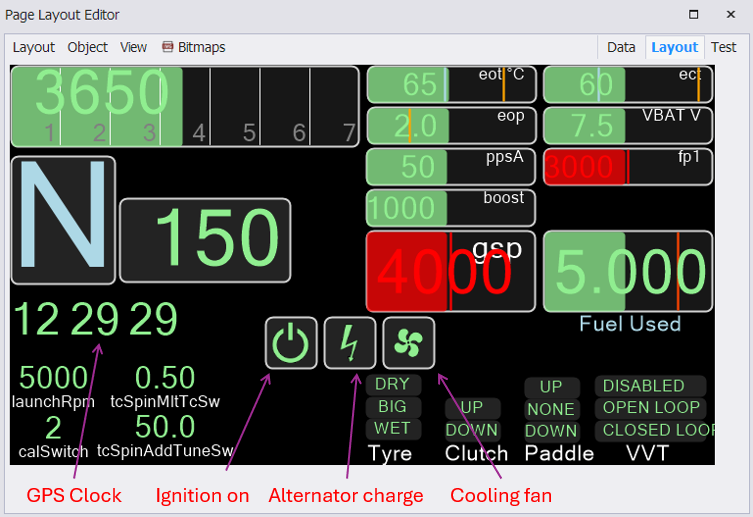
Exciting Shelsley
I dont know if you were following the live stream from Shelsley at the weekend, but the footage from the Hillclimb TV livestream was incredible. Alex Summers took the first run off win, and Matt Ryder the second. The footage can be seen here.Ethan nearly takes his first win
Ethan Faulkner, the teenager from N.Ireland, on his first visit to Pembrey, finished 2nd overall in the final run off on Sunday, beating several champions in the process. He's an amazing talent, and I look forward to seeing him in action at Mallory Park in just two weeks time. The EcoBoost is fuelled and ready......1June
Success in France for Will and Simon
I am really happy to report that Simon Bainbridge and Will Shuttleworth both had success in France at the St Goueno hillclimb over the weekend. Will's Radical SR3 is the one I rewired, for the Gen2 Hyabusa engine using the DTA S100 ECU and a donor loom from a car running a Zetec engine. Will had no issues at all over the weekend, and posted a very reasonable 1m 43s run on his final dry weather run on Sunday, before the rain spoilt the fun. Congratulations to Simon and Will on an outstanding job. When Will said in January he wanted to do the hillclimb in May, I was keen to get involved and help, and you couldnt ask for a better customer.31May
Dash upgrade completed
It turned out to be a very trivial change to get the ECU to recognise the data sent from the Plex dashboard. It was as I thought, that it needed a full 8 bytes of B Frame data, otherwise the frame would be discarded. With the Plex configured to send four rotary switches, plus the two digital paddles, and two more fixed values to pad the frame out to 8 bytes, I simply had to reassign the ECU IO to the relevant B Frames and it worked! Both paddles are recognised, along with all four switches. I also changed the Plex to send 0 to 11 for the 12 positions provided by the rotary switches, rather than 1 to 12, and the ECU recognised all the switch positions.I also unassigned the pair of analogue inputs on the SLAVE1 AN channels, which means I now have another pair of free analogue inputs available (via the X10 expander) which could be used elsewhere to monitor more of the engine health.
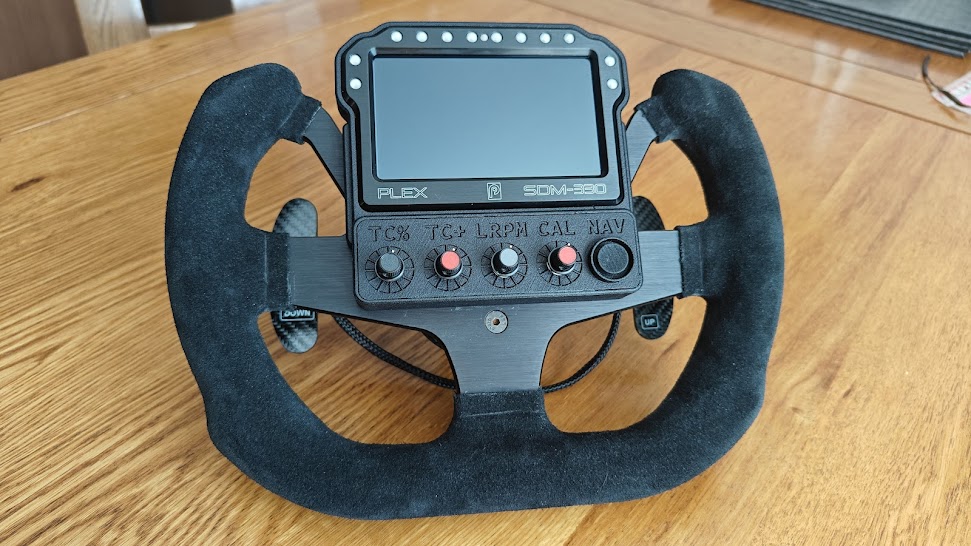
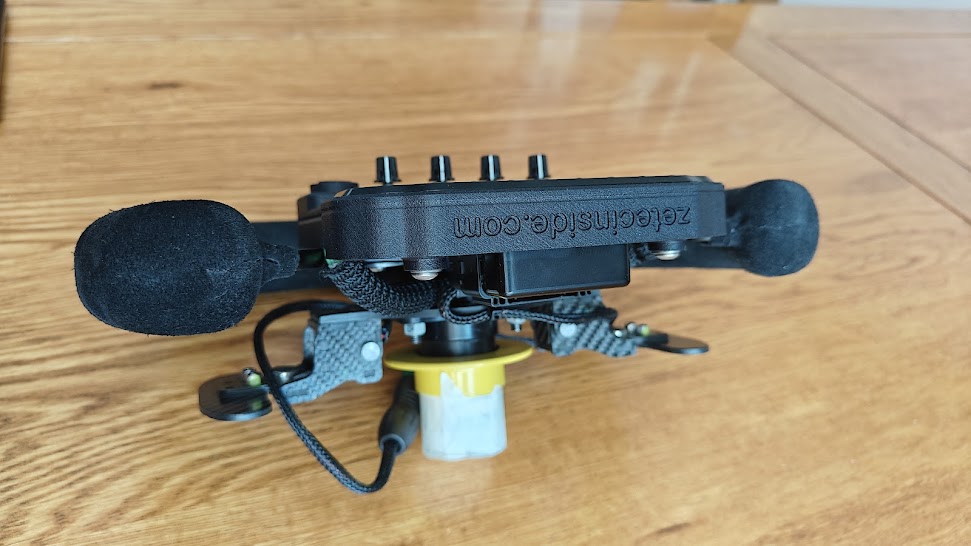
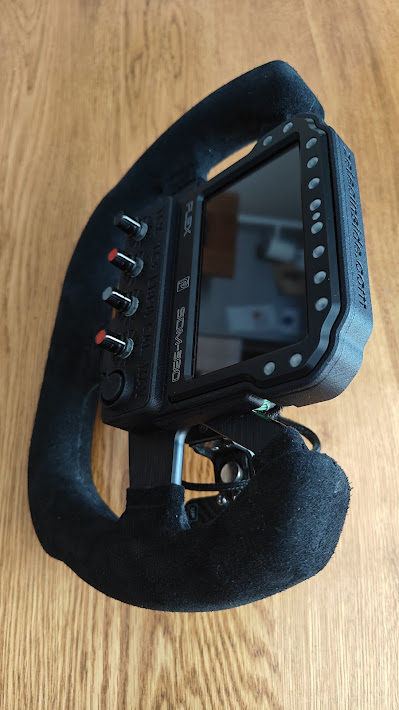
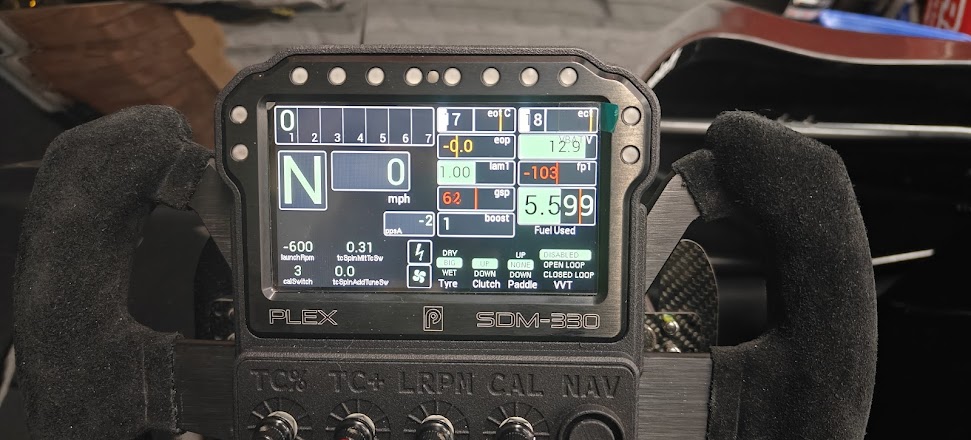
The printed bezel will be available in the Ebay shop, so if anyone else wants to use the same solution, I'm happy to manufacture and supply the parts.
26May
Connected the dash to the ECU
I had limited success connecting the Plex dash to the LifeRacing ECU. By that I mean, the dash displayed all the CAN data like I set it up to do. But the four rotary switches and the digital paddle switches were harder to setup. I'd asked Plex if the dash supported B frames, and it did. They provided the instructions how to send the LSB using a bitmask of 0x00FF. I set that up, but it wasnt receiving the data. To cut a long story short, the reason why was the ECU was discarding the B frames it was receiving, because I hadnt set the Plex dash to send 8 bytes. The ECU must see 8 bytes otherwise it discards the frame. Anyway, now I know that I've set the Plex up to send 8 bytes, and I'll try it again on Friday when I get back in to the garage again.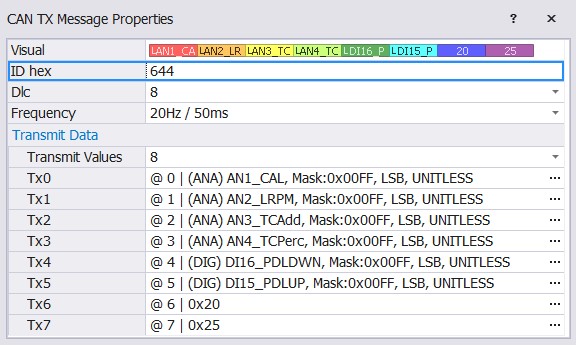
Because I've left the 9-way D-Type connector fitted on the CAN BUS, I can still plug the Dash4Pro display in at the same time as the Plex dash (which is connected using a Binder plug/socket) so that allowed me to display the frames being seen on the CAN bus. Very useful for debugging issues.
The BARC Midlands round at Snetterton in August has opened, and its another whopping £370 for the two days. Not quite as expensive as the Mallory Park round in June, but at least with Snetterton, you'll get more than two runs a day!
16May
Mk3 printed Plex dash bezel
The final version of the printed bezel was waiting for me when I got home on Thursday, so I didnt waste any time in taking the steering wheel apart and fitting the quick release boss and other parts to the new wheel. I think it looks great. I've just got a few wires to fit and it can be plugged in to the car for testing :DLink to the Youtube short.
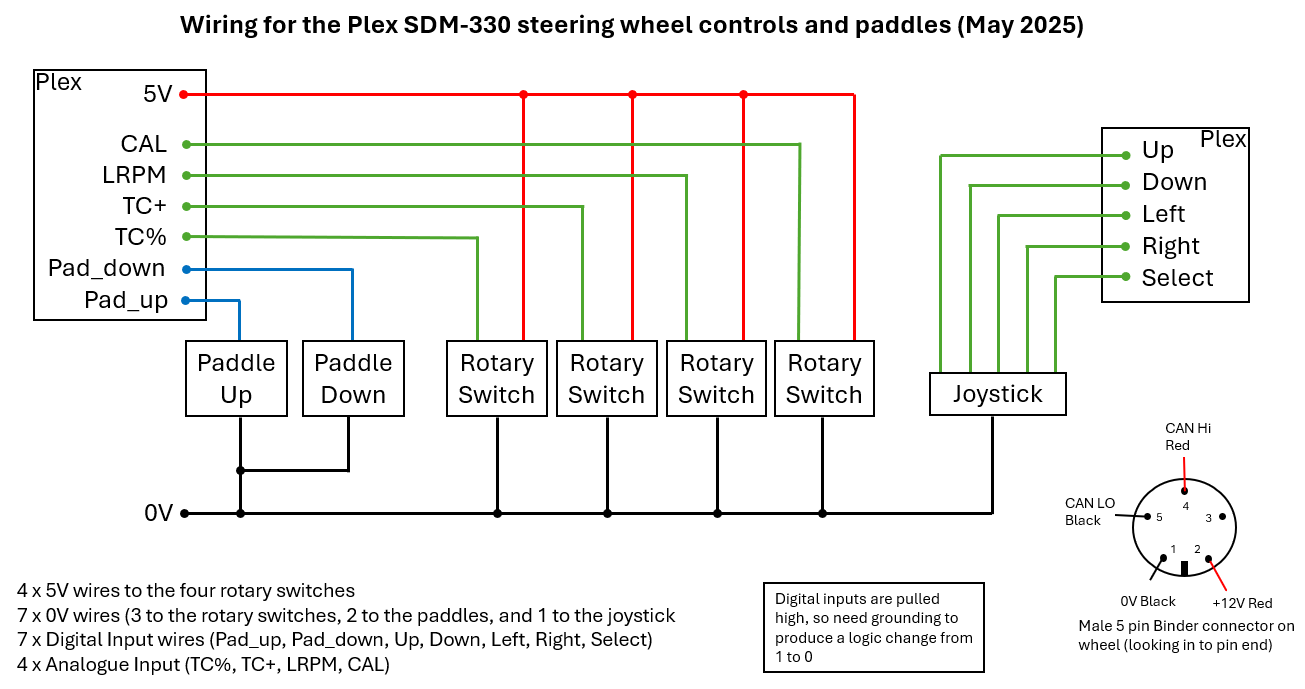
This is the schematic for the wiring that I need to produce to connect the four rotary switches, the joystick, and the paddles, to the Plex connector.
11May
Blyton success
I enjoyed myself sprinting at Blyton on Sunday, on the Eastern layout. Steve Miles and Martin Pickles (both BSC drivers) were both entered, but Martin had to withdraw and miss the event as he wasnt feeling well on Sunday morning. Get well soon Martin. Smileys ageing Van Diemen has had a lot of updates, some are working better than others. So he was my main (and only) competition, would he run the brand new Ultrasofts that he'd stashed in the trailer?I had a new silencer fitted, which I was hoping would knock a couple of decibels off the sound level, so I wouldnt trip the sound meter. After I returned from my first timed run, I was warned the sound level had broken 98dB. So the previous event it was 95dB, and the addition of the silencer made the car twice as loud? OK, so I removed the silencer, and dropped the auto-gear shift rpm for 3rd gear to 6000rpm, to act as a short shift. Still on the cleaned Avons, I did the first timed run, full of trepidation. Had I tripped the sound meter? No, I was below 95dB this time. How does that work? Why would a silencer double to sound pressure? Anyway I spoke to Kev Theaker, and he said keep left off the start line, to put a couple more car widths between your car and the sound meter, which I did, and for the next four runs, I had no issues with noise.
Smiley was running on old Pirellis, and I opted for the 3 year old Pirellis for my T3 run, and on that run I recorded my quickest time of 56.65s. For all the other runs I was in the 57's, once the Pirellis had had their first use, their grip levels fell away, but at least I was consitently faster than Smiles. His best run (his sixth run which I elected not to do) he managed a 56.72, so I beat him by 0.07s, to take first in class and fastest overall.
No drama's today, I did reconnect the water sprayer and used iced water, which kept the air charge temperature below 50C, which wasn't bad considering the ambient temperatures were around 25C.
7May
Dashboard housing update
I've made a final push to get the dashboard housing completed, by mirroring the chamber I added on the side for the wires, so there is now a chamber on both sides of the housing. This will give me more capacity for wires to run down to the front panel for the switches. I drilled the steering wheel at the weekend, for the Plex dash to attach to it, and the dash fits nicely inside the housing, against the aluminium wheel centre.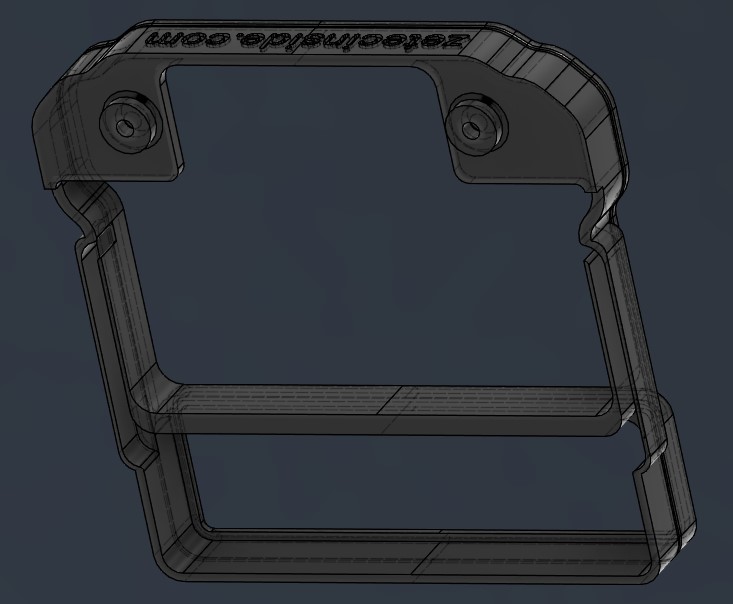
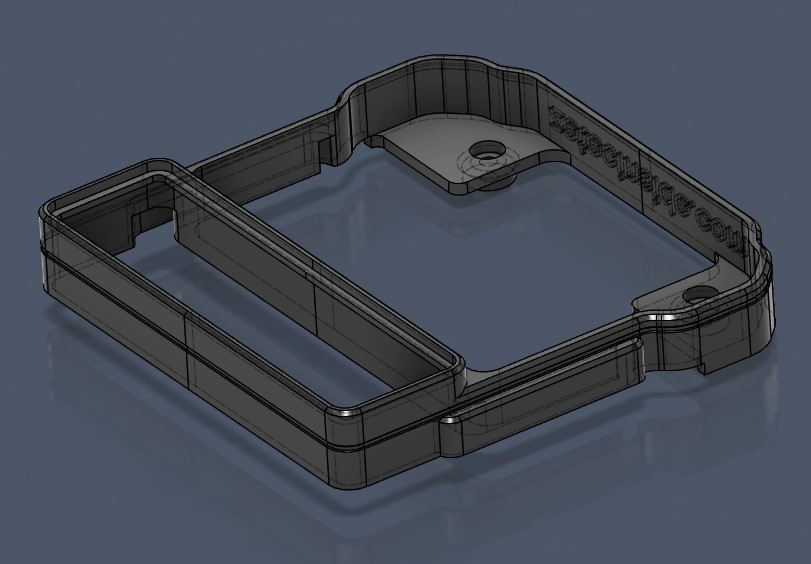
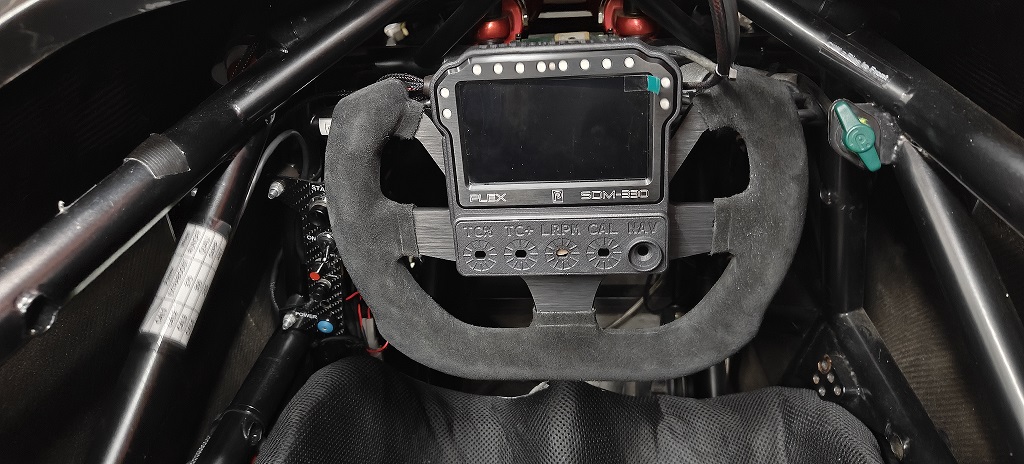
3May
Horn replaced
It was very easy to swap the faulty car horn on the beemer. Jack the car up, remove the wheel, remove the inner wheel arch lining, remove the faulty horn, and after fitting the new one, the process to put it all back together again took another 10 minutes. Cheaper than paying the BMW dealership to do it.2May
New job
I started a new 12 month contract on Monday, so now I'm working Hybrid so I'm spending three days a week at my clients office in Manchester, and two days at home. Its been a busy first week, with an unexpected trip home on Tuesday afternoon to return again Wednesday morning, so the mileage is double that of a normal week, but its good to get back on the road again, and back in to an office environment.I am now working as part of an Agile team, and getting to grips with daily SCRUMs and two week Sprints. Totally different mindset to the previous client I worked with.
I had the 335D serviced last week, in anticipation of the increased milage I'm going to be racking up. The last service was at the end of 2021, as the car had only travelled 14,000 miles in the past 3.5 years. So it was just a basic oil and filter change for £310. The dealer said one of the horns had stopped working, the car has a pair, a 400hz horn and a 500hz horn, and the 400hz one had gone silent (a common fault apparently on the 3 series). So I ordered a pair of new ones, made by Hella, from Autodoc, and they've arrived, ready for fitting this weekend.
27Apr
Latest ECU firmware introduces a User Timer
I was reading through the release notes for the most recent Life ECU firmware, and there is a User Timer feature which allows a timer to be started when certain conditions are met. For example, a timer can be started when the driven speed is above 0mph. Any two channels can be set as the trigger for each timer, the channels can be changed if you go in to the map customisation. And there are two User Timers that work independently. I asked Life for this feature over two years ago, and it shows how popular it was if they have now incorporated it in to the firmware.This would allow a User Timer to start when the run starts, and the same User Timer channel can be sent over CAN, as well as logged to the ECU data; so in theory you could send the User Timer value to the dash to display on the screen if you wanted to. Where that would be especially useful is if it were compared against distance from the previous fastest run, so you could see a delta. I might update the ECU to the new firmware (which needs bootcode 1.68) and have a play. There are also dozens of other improvements when the firmware is updated, adding even more flexibility for the tuner to eek performance from the car. Well done Life :D
23Apr
Rear wing fence repairs done
Nothing too difficult really, the sikaflex that bonds the pair of fences to the rear wing element, had deteriorated and the fences could move side to side. I removed all the red vinyl from the wing element, used masking tape to ensure the fresh sikaflex would have sharp edges to it once removed, and applied it, left it 24hours to cure, then removed the masking tape. I then spent a few hours removing all the adhesive left behind by the vinyl. The resin surface of the wing was then polished, and its all now reassembled and ready to be used at the next event in May.The Mallory Park weekend sprint in June, opened for entries this week, and its a whopping £400 for two timed runs each day! Thats 8 miles in total, at £50 per mile! Surprisingly, 47 entries have been received so far. The minimum number of entries is 75, and the maximum is 85, and given how slowly the event ran last year, it's going to be a very, very long weekend. The worst part is there is always a chance of a third timed run, and that prays on your mind. Will the second timed run be the only run off, or will there be another chance later on? The pressure just builds and builds all day. And then accidents happen.
One thing should have changed, and that is the placement of cones at the Edwina Chicane. If they're not on the circuit plan, they're not allowed to be on the track!
18Apr
Plex dashboard sending data over CAN video
13Apr
Onboard video
This is my 58s run from Sunday. The only difference between the way Javelin runs the event, compared to MUK, is they dont have a start line crew positioning the car on the start line. With Javelin a white pole is placed in front of the car, which you pull up to, and when the pole is lifted out of the way, thats your green light to go. Dead simple. No delays, just pull up to the line, and go when released. The rest of the course is the same length, with the same timing gear, and its timed to the undredth of the second, so its all the same as MUK events. There aren't cones littered around the circuit, they're in the same place as you'd normally find them. They have an ambulance, medics, marshals, and a well rehearsed Whatsapp group which tells you when to prepare to drive to the start line.I am hoping to run the new Plex dashboard for the next event in May, which is at Blyton back on the Eastern layout. I've dropped a silencer off with Altiss Engineering to see if Nigel can take some weight out of it, so I can drop the sound level by a couple of decibels. The silencer weighs 1.6Kg and I dont fancy driving over any bumps with an extra 1.6Kg hanging off the end of the turbo.
13Apr
Javelin success
I had a great day at Blyton with the Javelin Sprint series. The car was flawless, the front wing support brackets I designed worked perfectly, with no wing wobble, lots of downforce and a perfect aero balance. I couldnt have wished for more. I ran a 58.1 on the outer circuit on my 3rd run, all on the Avon HC3's, which is only 3seconds slower than my PB on Pirellis; given I'd not driven for 10 months, I was very happy with that time. The only issue with the Javelin Sprint series is the sound levels are lower than MUK events, because they use track day sound limits, and three times, whilst I was launching, I tripped the sound meter, with 95.4db, when the limit was 95db, and they deleted the three times. Luckily I had a 59.92 on the board, which gave me first in class and fastest single seater. I'll work on reducing the sound level for the next event in four weeks time, back at Blyton.The seat that TripleM made for me, was comfortable and held me very securely, and with the HANS device instead of the Hybrid HANS, I felt glued in to the car. I was careful to make sure that when I braked I lifted my foot clean off the throttle pedal, and I had no incidents all day.
On Saturday I replaced a section of UHMWPE which sits under the skirts, as it had worn at Mallory Park, and I also raised that section of the floor to give slightly more clearance between the strip and the tarmac, and it didnt bottom out all weekend.
With the gaps in the front wing, either side of the nosecone, allowing fresh air in to the side pods, the intercooler ran so cool that I disconnected the water sprayer, as its no longer required. I will leave it all plumbed in, in case on a hotter day, the ACT's rise again, but for yesterday it wasnt required at all.
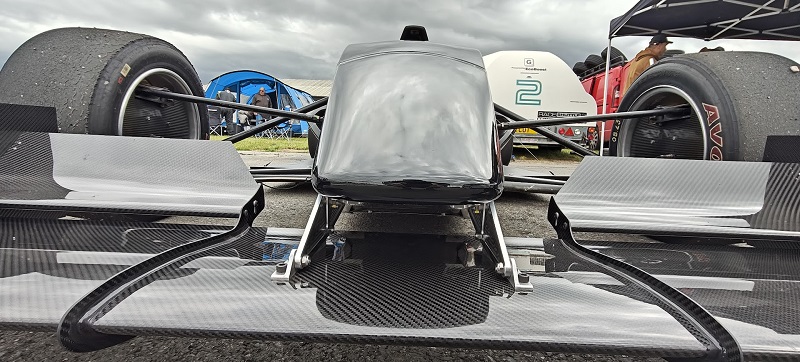
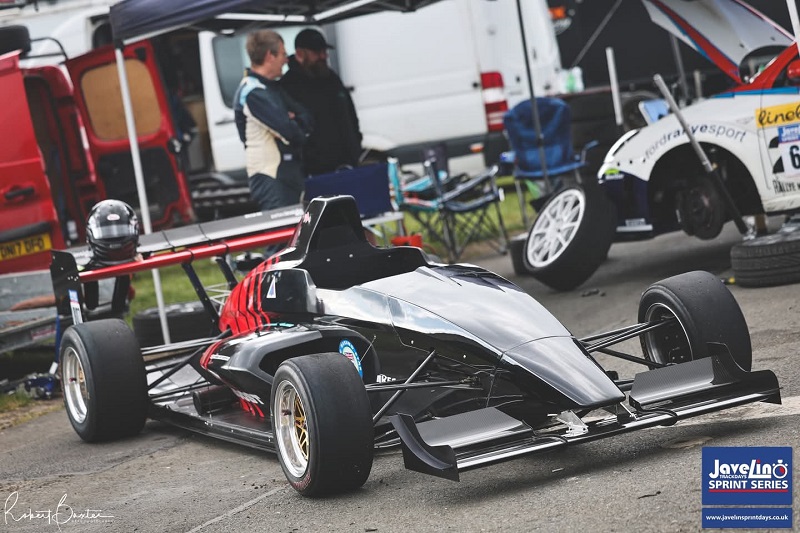
Air charge temperature and Ambient air temperature (red 2024 vs green 2025)
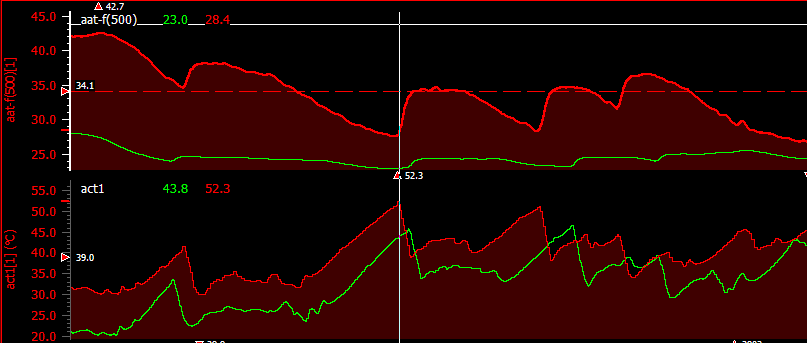
8Apr
Nosecone trimmed
I took the Dremel to the new Mygale nosecone to trim it underneath where it fits over the front wing drop plates. Now its sat where I want it, I can attach the fasteners to allow me to secure it to the bodyshell.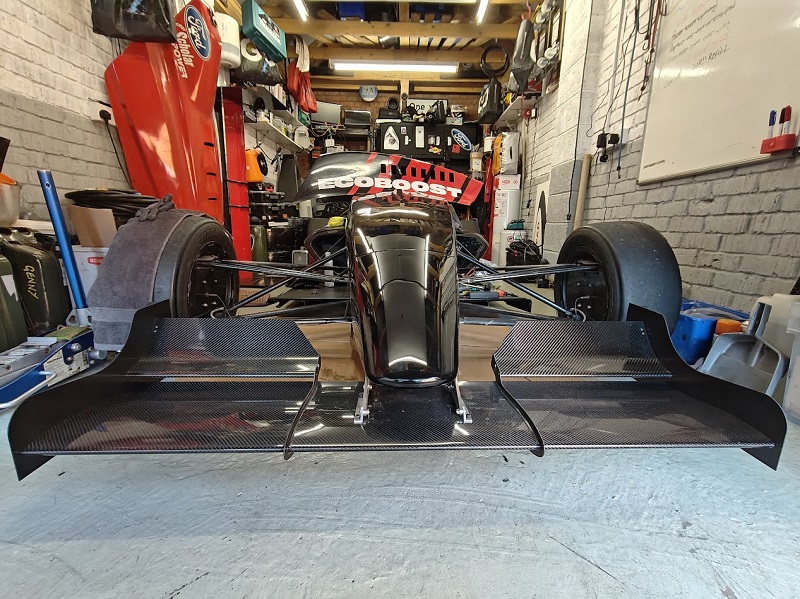
Yet more time spent on the Plex dash, trying to get it to do what I want. I've worked out how to convert kph to mph, using a math channel, and I can now get it to switch screens according to a User Flag that I've set. I like the whole User Flag concept thing. It allows you to set the flag to True or False based on the value of the channel. Its a neat way of managing whats displayed on the dash.
I've got one setup called Racing, which is True when the vehicleSpeed is over 22kph, and one called Pits which is True when the vehicleSpeed is below 21kph.
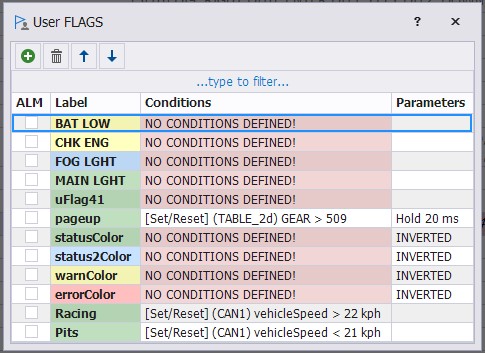
If you have a channel coming over CAN which is in KPH, its very easy to convert to MPH, in fact, you dont even need to convert it. The Plex software allows you to select MPH with a Numeric control, and it automatically shows it in Miles Per Hour. Nice.
Splash screen is also working, it is another tricky feature to work out. It says it will support JPG or PNG, but I havent managed to get JPG to load, PNG seems to be ok, but even then on one attempt when the image was set to load on bootup, the image caused the display to show garbage for a second instead of the picture I'd uploaded. With PNG, background transparency is supported, and it works too.
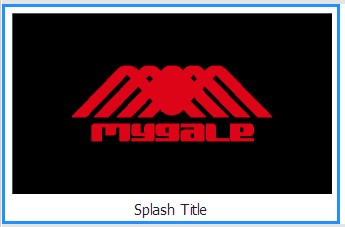
7Apr
Radical wiring complete
Last week I made the final trip over to work on the Radical SR3. I connected the NPN wheel speed sensors up to 12V, and they work fine with the DTA S100, which only needs 5V input on the speed sensors, but as Alex confirmed, 12V works fine. I then connected up the repaired rain light, and thats wired to a switch on the dashboard. Finally we worked through the dashboard switches for launch and traction control, and I wired in the 12 position rotary switch I made (with the resister ladder) and that now allows Will to go from 0 to 100% traction aggressiveness. He can also press a button to turn launch on and off, and I need to wire in a LED to give a visual indication that it is on, as the AIM dash doesnt show the status at the moment.I've sold another set of wheel speed sensor printed mounts to RLM, for use on their customer Cup cars.
I'm busy working on the Plex SDM-330 dashboard, changing the screen layouts to how I want them. I've connected my Raspberry Pi data injector, which sends ECU data over CAN to the display, and its working great at the moment.
I'm also getting the car ready for this weekend, which will be the first time I've driven it since the crash in June '24. I've quite a long list of jobs to work through and despite suffering from a very heavy cold over the weekend, I've made good progress. I'll need to visit Stoney Cove for some more compressed air before the weekend, as the dive tank doesnt have enough pressure to charge the paint ball bottle above 2500bar at the moment.
I collected the seat from Alan Mugglestone at Donington Park last weekend, and thats now fitted in the car, just the belt lengths to shorten to get it all comfortable and safe to sit in. Alan made it for me at the start of December, but he's been so busy it's taken 4 months to finish it. He gave me a free pass to get in to the paddock and I spent the day watching the GT Cup Cars, the Radicals, Legends and the Ford Focus Cup. Alan was running the Lamborghini of Grahame Tilley, and he also had the new Ginetta GTP8 in the garage, which is a great looking car. Its got a thumping great big 6.2L V8 under the bonnet!
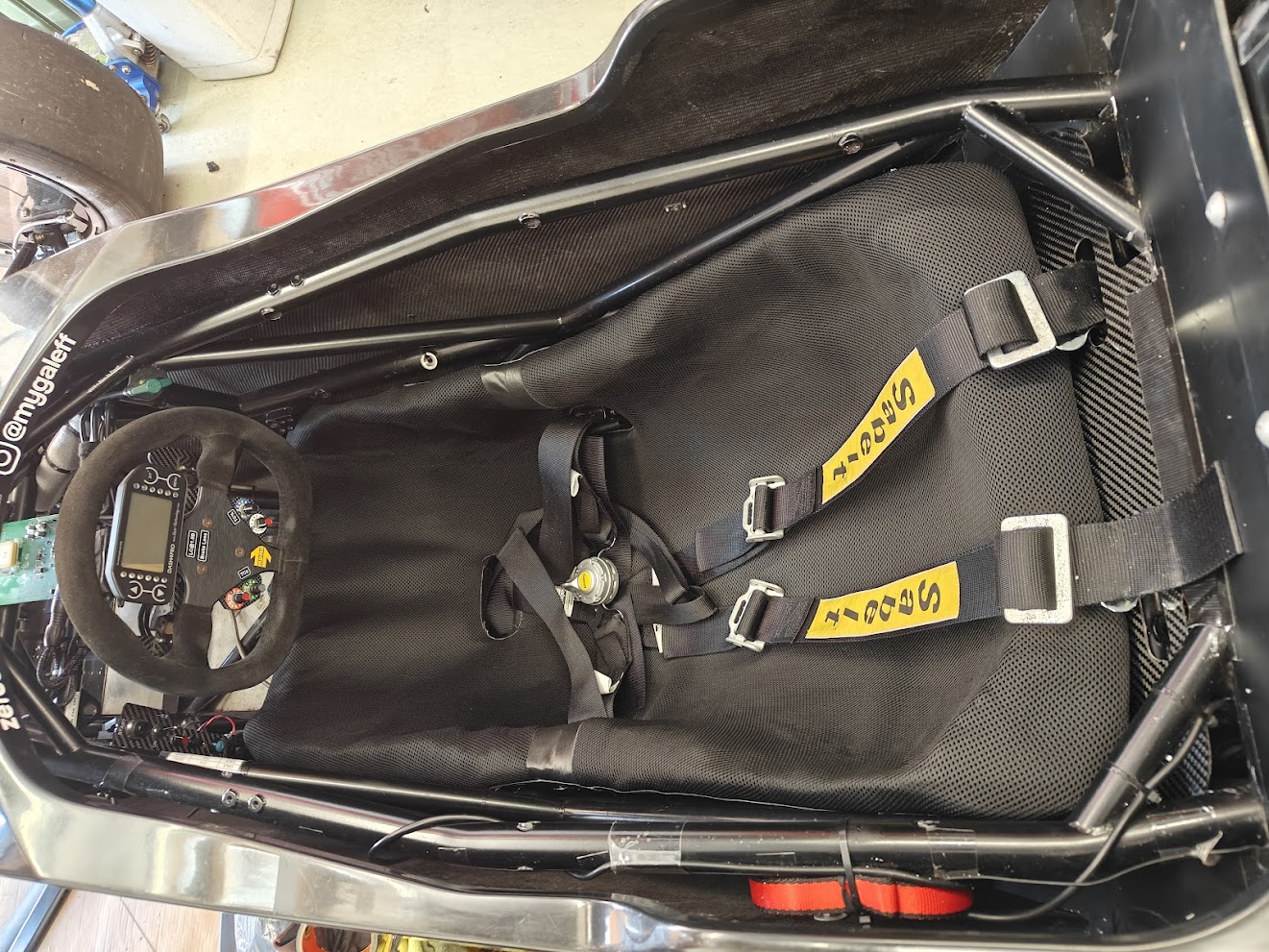
27Mar
Radical wiring (again)
Last night I managed to get the air compressor to run for the first time; it was providing a 12V feed to the relay via the pressure switch, so when the air pressure is low the pump is started. The relays were wired with a 12V feed and expecting a low signal (0v) to operate, so for the air compressor relay only, I've swapped the 12V feed for an earth, and now the pump runs and is under the control of the pressure switch.I wired in the 3 way DTM plugs on to the 12V NPN speed sensors, and couldnt get them to work. There didnt appear to be any supply voltage. I found a wire in the loom, labelled "Sensor power" which I traced back to the plugs, and sure enough it made a circuit. The question then was what voltage do we provide them with. The S100 needs a 5V pk-pk signal from the wheel speed sensors, and when I tried supplying 5V, none of the sensors detected motion from the wheels. Hmm, could they require 12V? Would that harm the inputs on the ECU? I asked Alex Chard (DTA) and he confirmed that running the sensors at 12V, and providing 12V to the wheel speed sensors, wouldn't be an issue. So I will wire the feed wire up to 12V and the ECU will hopefully be able to see the rotation of the wheels.
We then ran the engine for a few seconds, to check that the electric water pump was running under ECU control (it was) and that it was pumping water in the correct direction (it was). One last job was to fit the rain light, but when I was stripping the insulation back from the 12V wire to the light, the wire pulled out from the potting compound in the back of the light unit. When I got home I removed the potting compound from around the wires, and soldered two new wires on, and I just need to add some epoxy or black sikaflex back to the hole I made to ensure that the connections are water proof.
The final job was to check the paddles work, now we had air pressure, and configure the ECU for the 1-N-2-3-4-5-6 gear sequence from the bike box. That was quite easy, and then we struggled to find where the gear position voltages are set, for every gear. It wasnt in sensor linearisation, instead it was in Shift Cut. Once that was programmed in, the ECU showed the correct gear on the dashboard :D
25Mar
Repairs nearing completion
Last night I repaired the broken corner on the front bodywork where the nose cone attaches to the body. I mixed some resin to bond the pieces togeteher, but as ever, its too cold for it to cure in the quoted 60 minutes, so I'll give it 24 hours and see what its like tonight. I also fitted the aero section back in to the intercooler side pod, which for some reason I'd never refitted after swapping to the larger intercooler. It fits well, just needs a slight trim along one edge, so I'll get that done and refit the cowling tonight.The Plex dashboard is on its way from Greece. I am expecting it to replace the ECUMaster CAN switch board that sits on the back of the steering wheel, and relays the paddles and rotary switch positions back to the ECU. The Plex has plenty of digital and analogue inputs, and should be able to present the switch status rapidly enough for the ecu not to miss a paddle switch change. I'll set the polling frequency to the same as how it's setup in the CAN switch board.
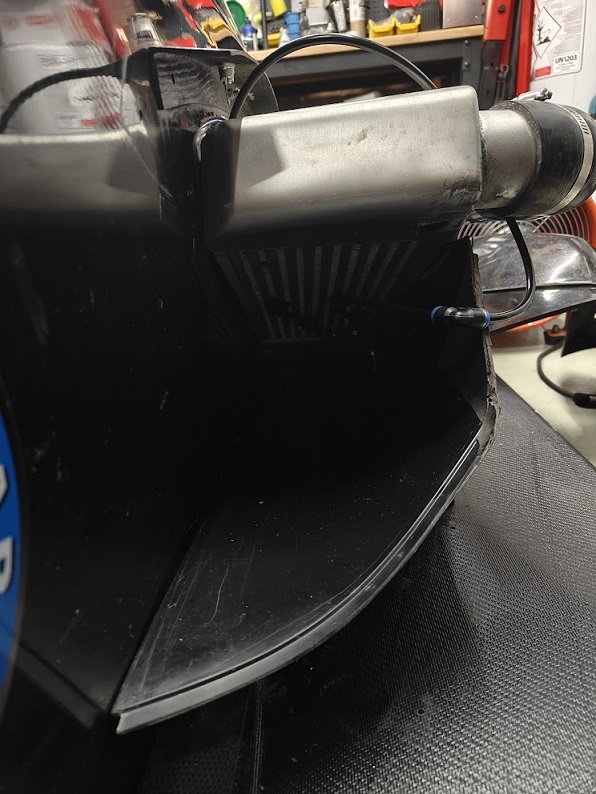
24Mar
DTM plugs ordered
I've had to order another set of DTM connectors for the Radical SR3 wiring loom, with 20AWG pins, to connect to the four leads that take the signals from the wheel speed sensors to the ECU. They should be with me for Thursday, hopefully sooner so I can complete the job one evening after work.The link to the Youtube short showing the engine running is here
22Mar
The Hyabusa Engine runs
Another trip over to work on the Radical today, and after swapping the fuse box for a version with 12 fuses, then loading the calibration which I'd modifed using the cal supplied by Alex Chard of DTA, we filled the dry sump tank with oil, and with the spark plugs removed and injectors unplugged, primed the system until it produced 1.5bar of oil pressure on the key; we then went for an engine run, and with some manual throttle, it started on the first push of the button and ticked over smoothly. Oil pressure was 6bar, and there were no issues.I then wired in the rectifier output (with 25A inline fuse) across the battery, so it would charge the battery when the engine was running. I also wired in a switch on the dashboard to cut the power to the ignition circuit, which allows the engine to be stopped without losing power to the ECU. I wired in the air compressor too, so ready to be tested. The IGN switch tested out ok on the next run, as did the charging circuitry.
I'm very happy its worked so well, and all I need to do next is to wire in the wheel speed sensors, and make some more changes to the dashboard to hook up the few remaining switches which are used for launch and traction control. I need to check the water pump runs too, as thats on Aux6 and it wasnt enabled by default as the previous owner of the ECU didnt run an electric pump. Its a shame the ECU doesnt drive the pump using PWM, as it will be on all the time, rather than running at a slower rate when the engine is ticking over.
This is the scope output from the DTA SWIN software, showing the pulses received from the magnetic crank sensor, with the engine spun over on the starter motor. Nice and clean.
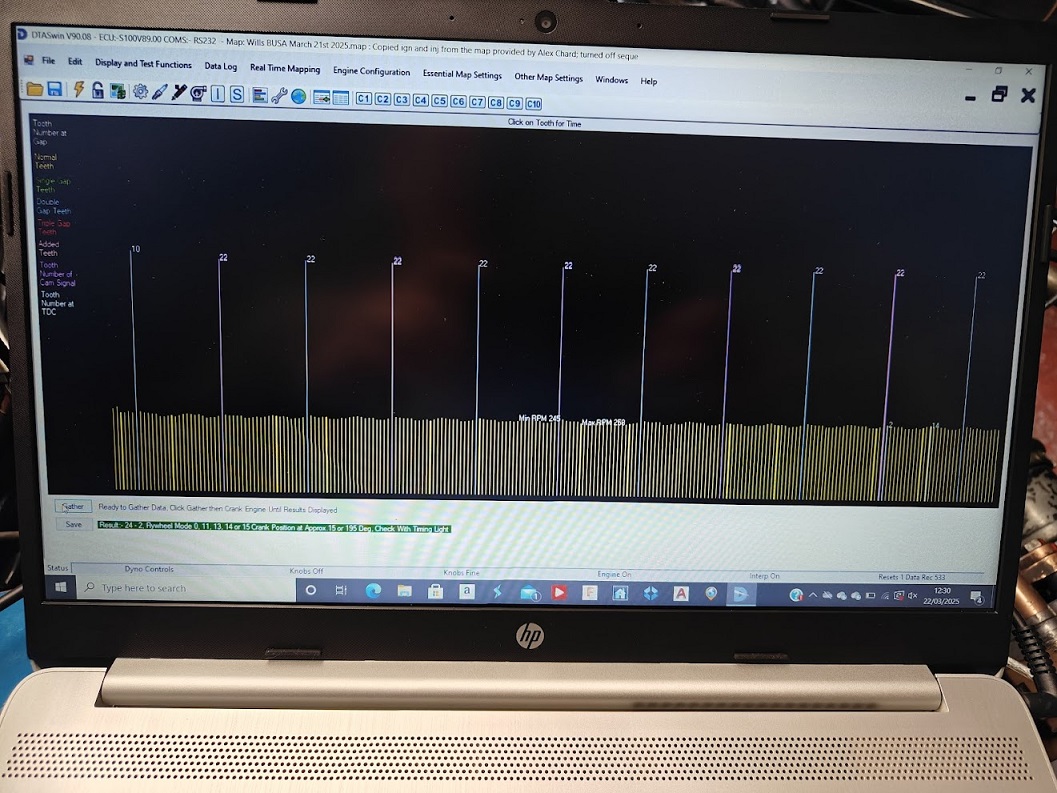
18Mar
Lambda connected
I wired in the Innovate LC2 wideband controller tonight, and used the Yellow (Analogue output 1) wire to pin 19 on the ECU. This is the wideband output. The ECU was then configured to use the Innovate LM1 sensor, and it showed a rising AFR which topped out at Lambda 1.5, which is quite normal when the engine isnt running. I also wired in a launch control button, which for some reason the ECU couldnt see, so I need to investigate where on the ECU the pin goes back to to work out why its not being seen. We are changing the fuse box from a 6 fuse to a 12 fuse version, as we've already run out of fuses for the different circuits. I've ordered a 12 way rotary switch and 470R resistors, so I can build a traction control switch for the front panel. If the parts arrive tomorrow I'll build it up for fitting on Saturday.17Mar
DTA map updated
The ECU in the Radical came from a car running a 2.0 Zetec, so the ignition and fuel tables all needed modifying. Alex from DTA kindly provided a map for a Gen 1 Busa, so I copied over the fuel and ignition tables last night, and set the number of teeth on the crank sensor wheel to 24 with 2 missing. I've also setup the Lambda parameters to use the Innovate LM1/LC1, and setup things like the RPM range (0-10500), Engine Start Fuelling tables, etc, and I've turned off sequential injection and sequential ignition until we have got the engine running, and then they'll be tried.16Mar
Another day of wiring on the Radical
On Saturday I connected up all the relays to the DTA ECU on the Radical SR3, and the ECU can now control the radiator fan, water and fuel pumps. We performed tests on all the outputs and everything worked fine. I rescaled the water temp sensor to Suzuki K5 and it now reads the correct temperature. I ran in to difficulties figuring out the wiring to the 5 wire Bosch LSU4.9 Lambda, so I left it alone, and checking today with Alex at DTAFast, it transpires we have bought a wideband sensor, and the DTA S100 doesnt work with wideband (I should have remembered as I had an S80 on the Fiesta with the LC1 wideband controller) so we've had to order the Innovate LC2 wideband controller, which will drive the five wire wideband sensor, and provide the ECU with a linear signal showing the Oxygen content of the exhaust. The older 4 wire narrow band sensors only provide a lean/rich signal, so thats a good reason for going for the wideband version. Another issue was the connector on the new engine oil temperature sensor, which was meant to be a mini-timer but was a totally different oval/rounded 2 pin connector, so thats going back and will be swapped for the mini-timer version. So all thats left to do is to connect the lambda, and run wires from the switches on the dashboard to the inputs on the ECU for the launch control, traction control and wet/dry map settings, as well as a switch for the rain light. I ran a pair of wires to the microswitch we're fitting on the clutch pedal, which will allow first or reverse to be selected as long as the clutch pedal is depressed first. Oh and the wheel speed sensors need plumbing in, which is another very straight forward job.When we went to fit the 73mm printed wheel speed sensor rings to the output cups, we realised we couldnt slide them on because there is a raised lip/section to the end of the cups, which would have required a larger diameter than 73mm to slide them over. So we cut both the rings using a thin blade hack saw, slid them on, and used sikaflex to bond the rings on securely. In the mean time I have redesigned the rings to allow them to be slid over the end of the cup, and then locked in position using an M2.5mm x 5mm socket head screw.
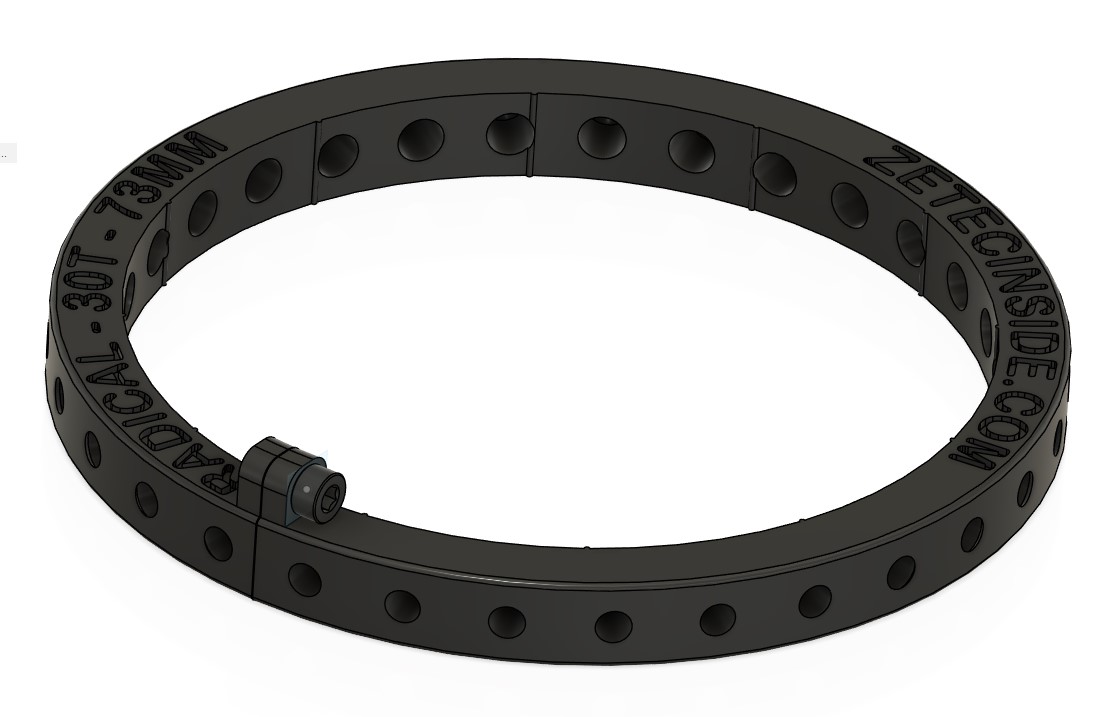
I've sent off the bezel and two different front panels for 3D printing, as well as the Mk2 73mm rings, delivery should be in two weeks time. Meanwhile, there is still no sign of the seat from Triple M, or the fresh Pirelli tyres, and my first event at Blyton is on April 13th...
14Mar
Plex steering wheel bezel re-designed... again...
I've made the bezel more versatile by allowing for the front switch panel to be interchangeable. This will allow me to change the switch layout and print a small panel which will then fit in to the front of the bezel. I think now I have finished the design, finally, unless I suddenly think of anything else.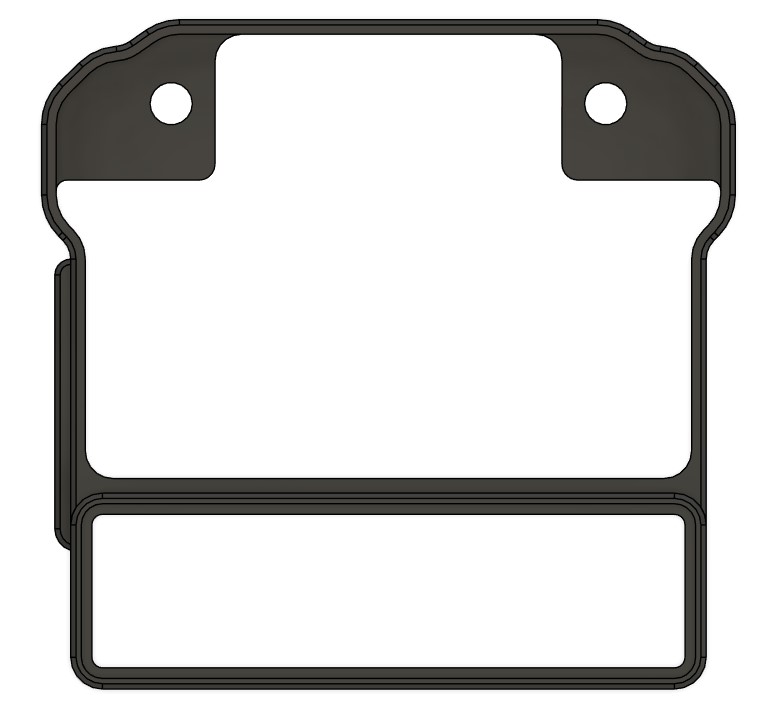
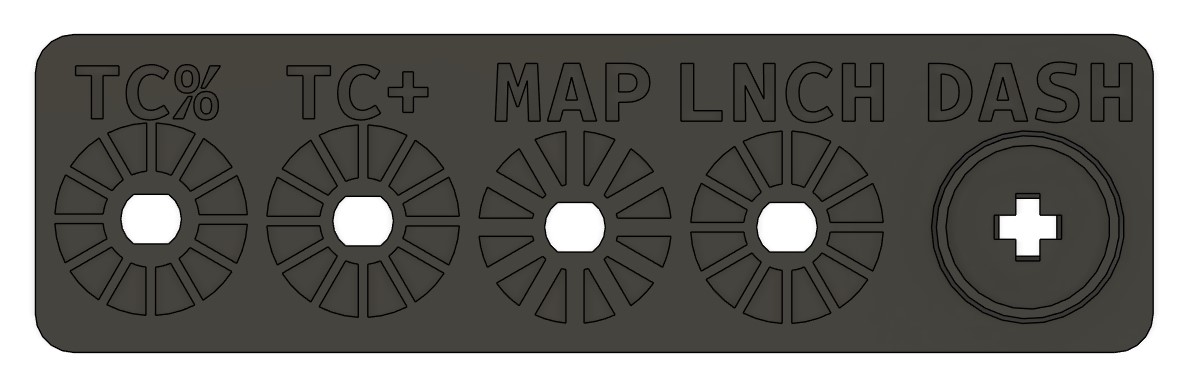
13Mar
Plex steering wheel bezel re-designed...
I found a 5 way hat switch that I'm going to use instead of the three buttons, for navigating the screens on the Plex dash. This will allow Up, Down and Back navigation, and when the switch is pressed down, that will provide the Select signal. I've redrawn the panel that fits in the front of the bezel, and I may print it seperately to the bezel, which will allow me to replace the panel if I decide to redesign it for additional switches.
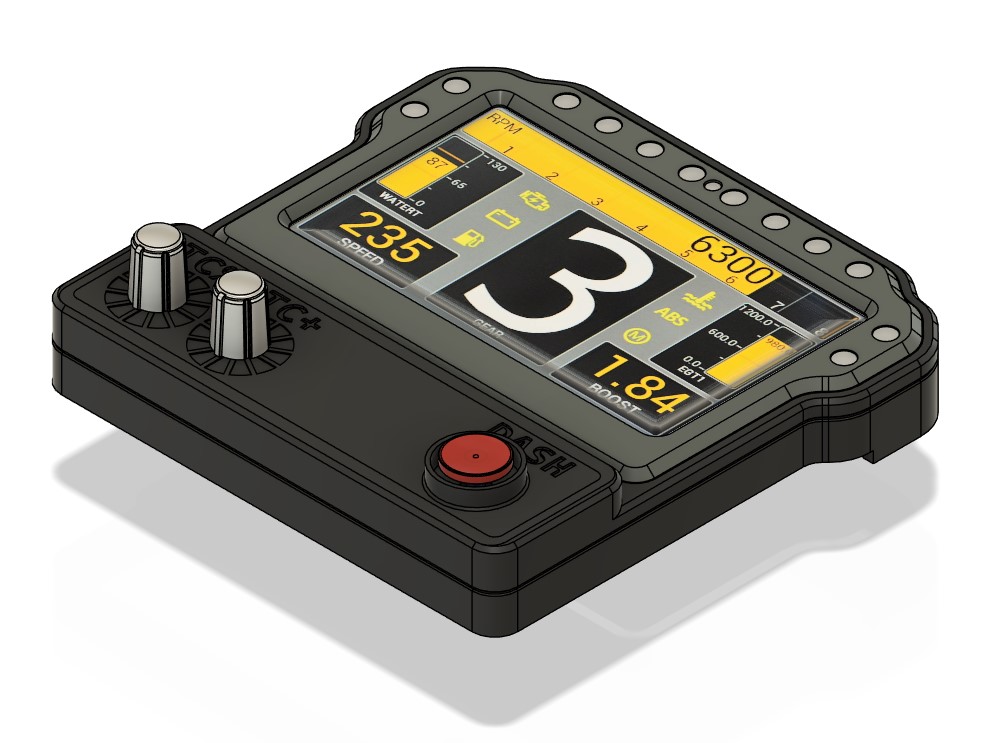
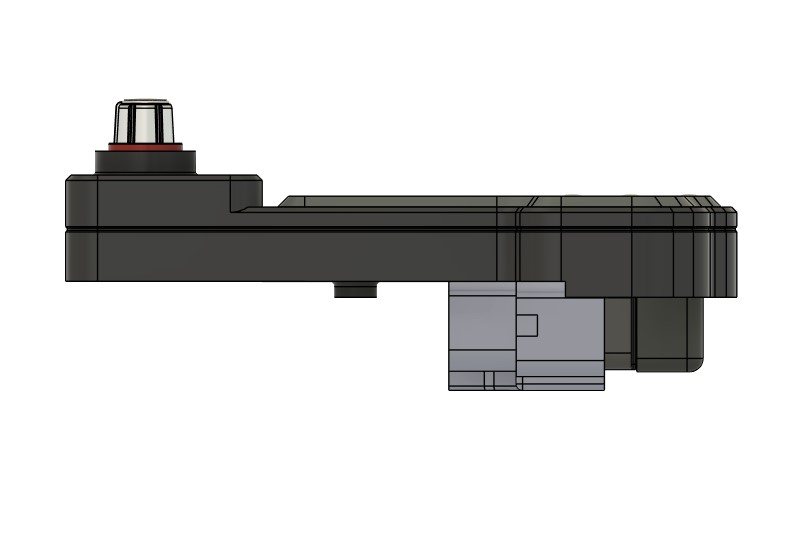
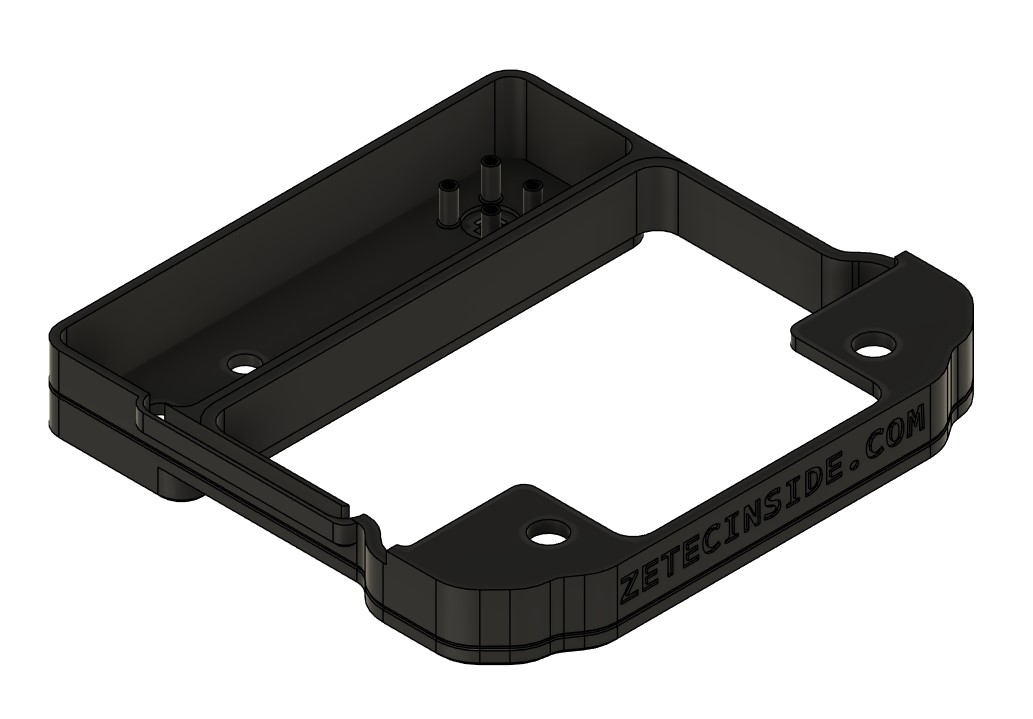
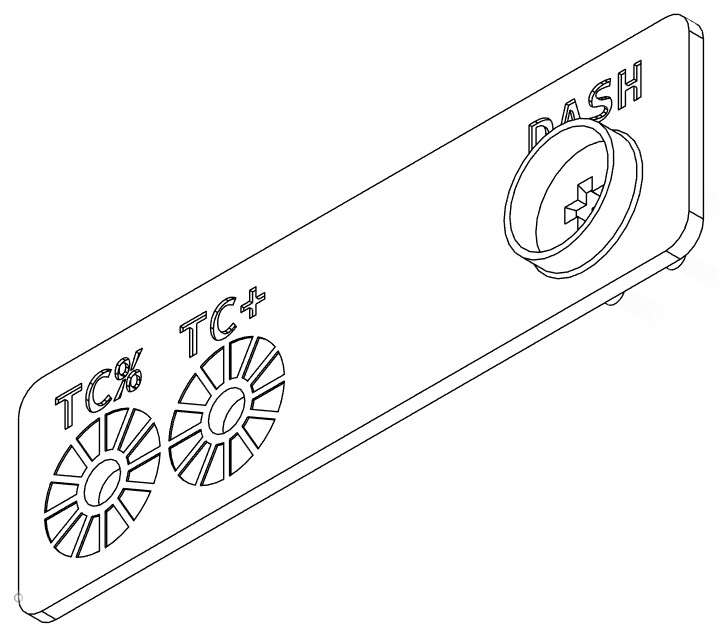
10Mar
Plex steering wheel bezel designed...
This took a few hours to put together. The bezel attaches to the Plex SDM-330 which itself is bolted to the steering wheel. I'm on the lookout for a rugged hat switch to allow me to replace the three buttons that operate the display options. My son's Walksnail FPV head set has the very thing, on the side, which allows the menus to be navigated, and options selected by pushing the button down. Thats exactly what I need, and I'm now on the hunt for one.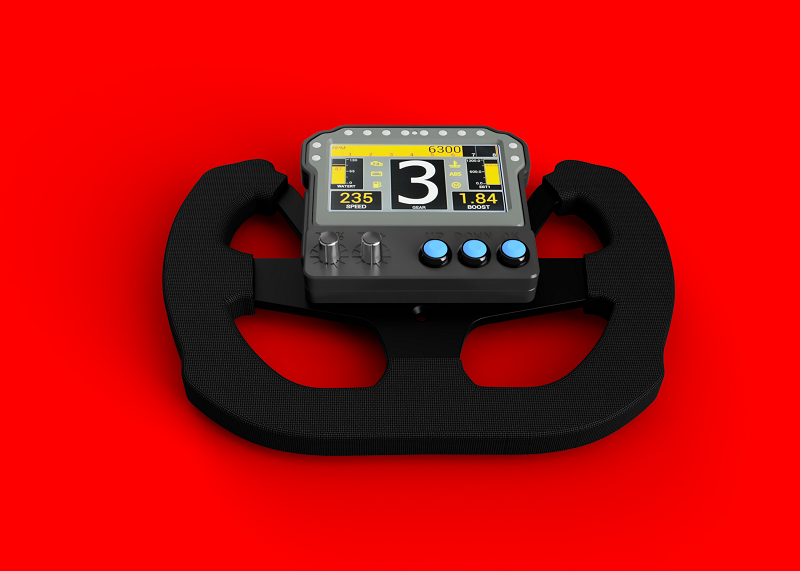
This is how it should look fitted to the wheel. Excuse the crappy drawing of the wheel, the real thing is far more attractive LOL
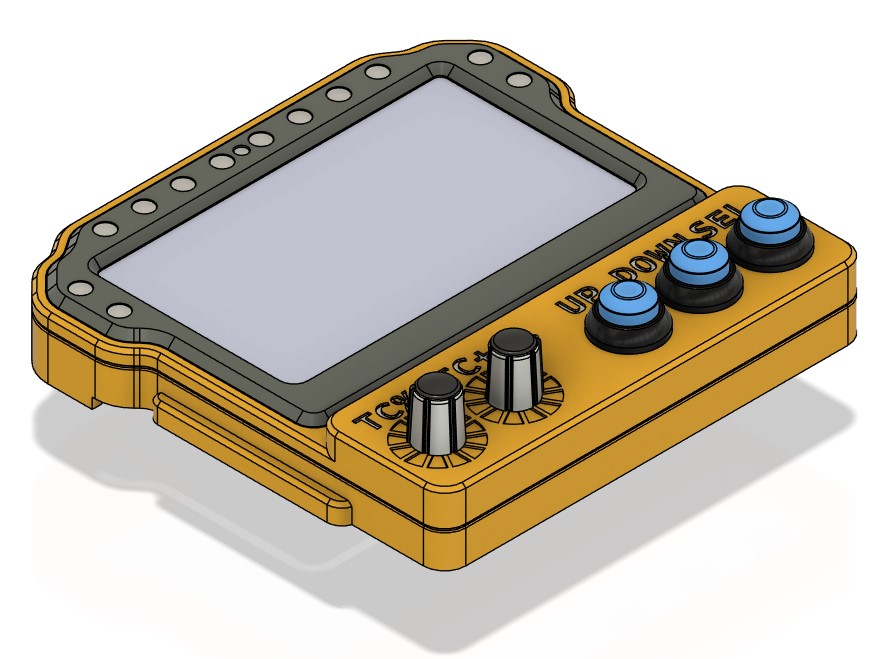
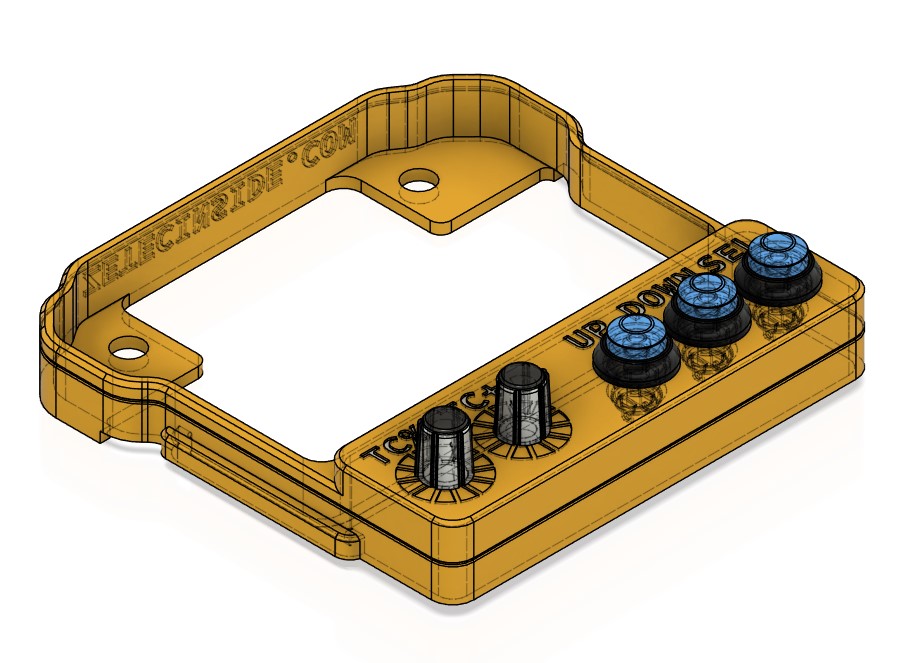
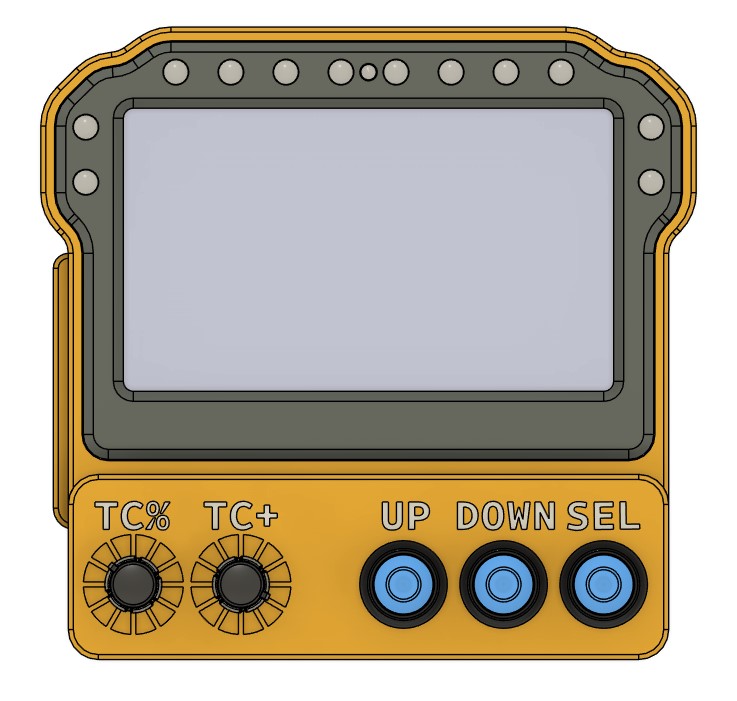
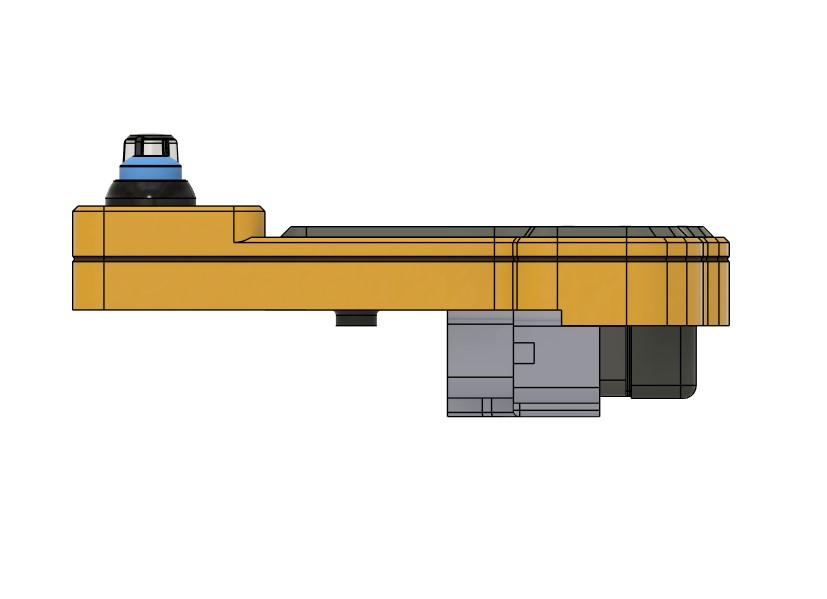
9Mar
Day 3 of wiring on the Radical
On Saturday I continued with the wiring on the Radical. I added an air temperature sensor, gearbox oil temperature, and wired in the water pump, radiator fan, and the fuel pump. I also swapped the pins around for the fuel injectors to match the same firing order as the COP's. I powered the dashboard up too, to see if the CAN data from the ECU was being received, and it was :DThe relay block is now fixed in place, and I ran out of locking 6.3mm spade terminals which prevented me from connecting up the fan and both pumps, but that should be completed next weekend. For some reason the Busa engine coolant temp sensor is reading 87C at ambient, but I think that could be down to the sensor scaling, so I'll see if the sensor is working and try to recalibrate the ECU for it.
I ran the engine today for the first time since it was switched off in June after the crash. I needn't have worried. First push of the button and it started. No horrible noises, no drama, and very little smoke from the exhaust. I ran it for 15 minutes to let everything warm up. The link to a Youtube short of her running is here VIDEO
1Mar
Day 2 of wiring on the Radical
On Saturday I spent another day working on the wiring loom on the Radical. I now have the 3 wire cam sensor connected to the DTA S100 ECU, as well as the fuel pressure sensor, and the gear position sensor. I also swapped the connections over for the COPs, so they fire in the correct order.The BUSA Gen2 engine has a firing order of 1243, so
COP1 goes to Pin 10
COP2 goes to Pin 18
COP3 goes to Pin 26
COP4 goes to Pin 1
Not forgetting that Cylinder 1 is at the same end of the engine as the CAM Sensor.
I found some fatigued wires inside the ECU connectors too, the analogue 5V connection split in to four wires, to provide 5V to four sensors, and the crimp that brought all the wires together was frayed, so I remade the connection, and added another four more wires for expansion; the same thing was done to the sensor ground wire, so I remade that connection and added four more wires.
This coming Saturday we'll be connecting up all the outputs using a relay block, which has four 12V 30A relays fitted already. I'll be connecting up the Fuel Pump, Water Pump, and the Radiator Fan. As well as the Dashboard, Steering Wheel paddles, and anything else thats left.
I've also designed a 30 dowel 73mm speed sensor ring for the car, which is away for printing.
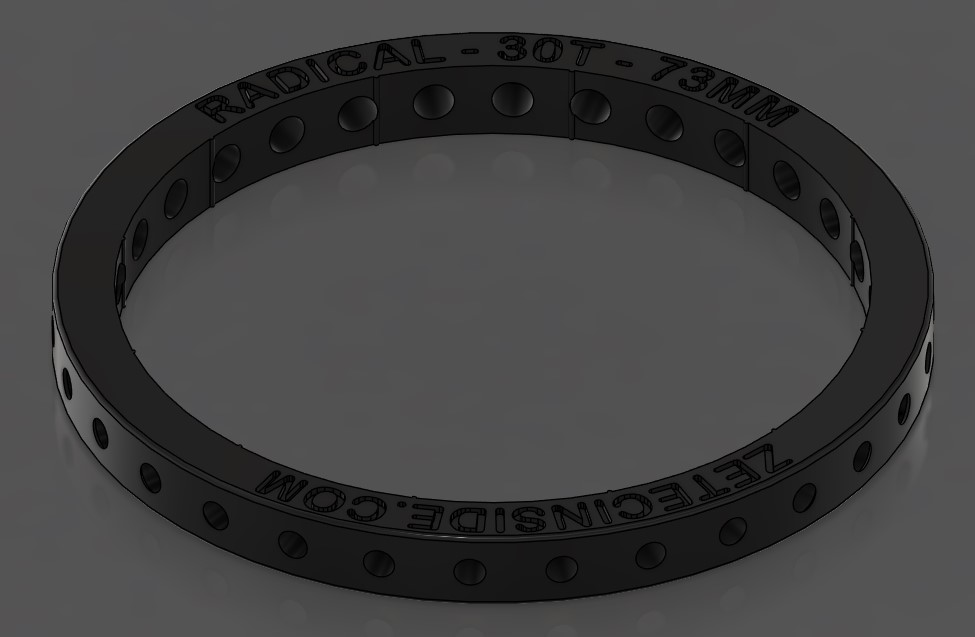